What to know: In March 2027, many existing facilities will need to submit to the Environmental Protection Agency facility response plans for managing worst-case discharges of certain hazardous substances. Early preparation is essential to avoiding last-minute compliance challenges.
Beginning in March 2027 — or earlier in some cases — many facilities will need to submit to the U.S. Environmental Protection Agency (EPA) their plans for managing hazardous substance discharges. For lean and busy environmental departments, this new requirement may seem like something to tackle after other, more-urgent priorities. But determining whether the rule impacts your facility requires preparation, and starting that work now can save headaches in the future.
What is the facility response plan requirement for hazardous substances?
The Clean Water Act (CWA) Hazardous Substance Facility Response Plan rule (promulgated on March 14, 2024) closes a gap governing facilities that use and store hazardous substances. The CWA previously did not require many of these facilities to have a discharge response plan in place. Under the rule, facilities that meet certain requirements must submit a facility response plan (FRP) that details preparation for managing a “worst-case discharge”— i.e., the largest discharge possible in the worst conditions possible — of any of the more than 60 hazardous substances regulated under the CWA.
Who does the new rule affect?
Large or complex industrial and manufacturing facilities will likely feel the impact of this rule most acutely. It applies to any facility that meets two broad criteria:
- The facility is located within half a mile of navigable water or a conveyance to navigable water. The rule aims to keep hazardous substances out of water supplies in the event of a spill.
- The facility uses or stores any CWA-listed hazardous substance at 1,000 times its reportable quantity. A variety of industries and operations use these substances, including for metal plating, aircraft maintenance, electronics manufacturing, and industrial-scale wastewater treatment, so the applicability is broad.
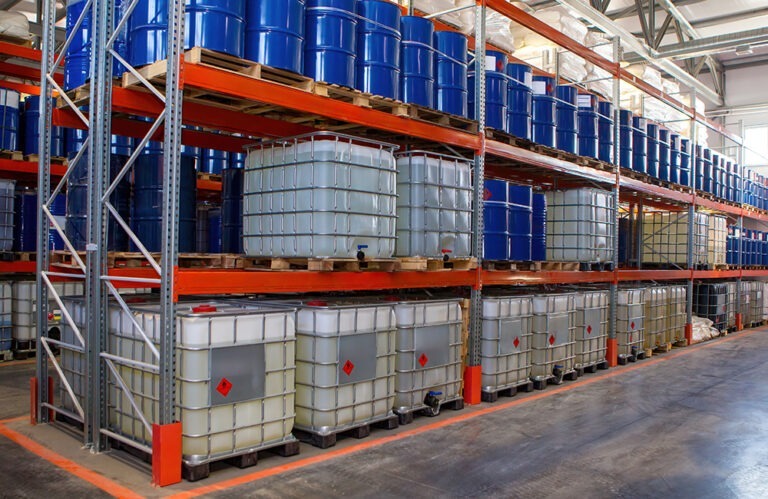
How can facilities prepare?
Determine whether the rule applies to you. A facility must meet both criteria for the rule to apply. Many nuances exist within those criteria, though, which makes it important to start understanding the potential application to your business soon.
- Distance to waterways. This aspect is fairly straightforward; if you’re not located within the required distance to navigable water, you’re exempt. The EPA defines navigable water in the statute as “the waters of the United States, including the territorial seas.”
- Inventory of hazardous substances. Here’s where it gets more complicated. Safety data sheets tell you what chemicals your facility has on-site, but you also have to calculate the total amounts of each of those chemicals. If any of those total amounts exceed the CWA’s reportable quantities, you will likely have to submit an FRP.
Common CWA-listed hazardous substances
- Acetic acid
- Ammonia
- Arsenic
- Benzene
- Chromic acid
- Formaldehyde
- Hydrochloric acid
- Lead and its compounds
- Mercury
- Nitric acid
- Phenol
- Sulfuric acid
- Toluene
- Xylene
If you have a pure hazardous substance on-site, the quantity determination is simple. However, the amount of a hazardous substance in any mixtures also counts toward the total amount. Safety data sheets give a percentage range for the amount of each component in a mixture; you must assume the high end of the range when calculating the cumulative total amount on-site.
For example, we recently conducted an audit of an airline facility’s on-site hazardous substances to understand whether it would need to comply with the new rule. We began by listing each of the hundreds of chemicals on-site. Then we determined which mixtures contained CWA-covered substances. For each of those, we completed calculations to determine whether total amounts exceeded reportable quantities.
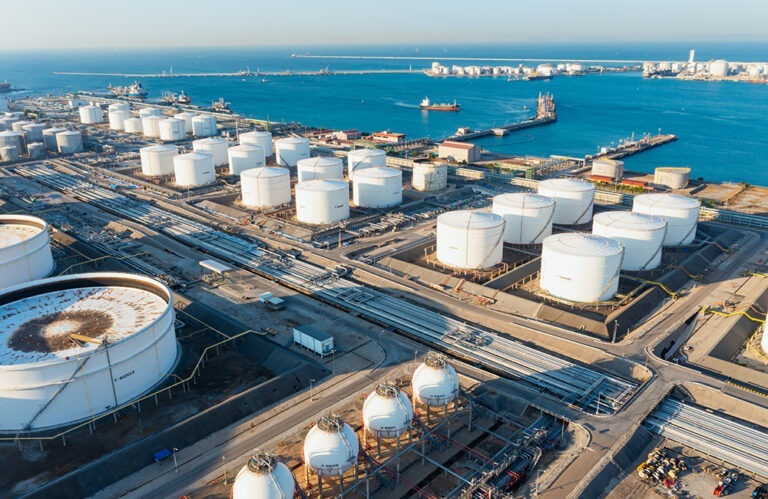
Of course, a facility’s environmental team can perform these calculations themselves, but finding the time to do so can prove challenging. When a facility houses hundreds or even thousands of hazardous chemicals, cataloguing the amounts of each can take weeks — time that busy environmental teams often can’t spare.
- Eligibility exceptions. Even if a facility meets both criteria, it might fall under one of a few exemptions to the new rule. It matters, for example, whether the hazardous substances at a site are to be used for processes or products or if they’re wastes from those processes or products. And although this rule impacts a broad swath of industries, chemicals in retail; janitorial; and food, drug, and cosmetic operations are generally excluded.
Also, how facilities store the hazardous substances matters. If they are stored in underground tanks and/or moved via underground conveyances, they pose less threat to surface water and therefore may not need to count toward totals.

Determine your compliance deadline. Most existing facilities will have until March 14, 2027 — 36 months after the rule’s effective date — to submit their FRP. But some exceptions exist that can impact how you plan for compliance:
- If a facility plans to bring on-site a new chemical at above the reportable quantity, you must have the plan in place before that chemical arrives.
- If you’re modifying the facility or starting new operations, an FRP must be in place before modifications or the new operations start.
- If you’re building a new facility that will fit the criteria above, an FRP must be in place prior to start of operations.
Get the right guidance. Once you’ve determined whether you must comply with the rule, you can start working on an FRP. Facilities with existing spill prevention, control, and countermeasure plans may have a head start, as some requirements overlap. In general, FRPs will require documentation of the location of hazardous substances, discharge detection methods, response and notification procedures, evacuation plans and coordination with local emergency personnel, and training details.
Environmental teams or consultants such as Haley & Aldrich can assist with preparing plans and evaluating compliance needs. But the key to managing this requirement now is first to know it’s coming and that March 2027 is closer than it seems.
Contact the authors to learn how Haley & Aldrich can guide your response to the new rule.
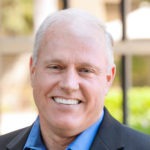
Senior Associate
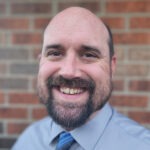
Project Manager, Environmental Engineer
Published: 7/18/2025