The U.S. offshore wind industry is poised to take off in early 2021 with the likely approval of the Vineyard Wind project. This will signal the start of construction of multiple proposed windfarms. The offshore wind turbines being considered are massive, with blade spans of over 200 meters, and present an equally massive onshore challenge. The main turbine sections will be manufactured onshore, loaded onto large construction vessels, and floated upright to the installation location with the final assembly of other sections occurring at sea. Project teams will need ships to execute this work, including those needed to conduct surveys, lay the array and export cables, construct offshore substations, and ferry workers and equipment to and from the offshore construction sites. As a result, this will require state governments and developers to make significant improvements to port and harbor facilities in the Northeast.
Most U.S. ports lack the area required for manufacturing and marshalling these massive components, heavy wharfs to accommodate the offshore construction vessels, and infrastructure to move the manufactured sections to the ports. What’s more, the manufactured towers and turbines shipped upright at over 260 meters high require a port with open ocean access unobstructed by bridges or overhead powerlines, and the water depth to accommodate these large vessels.
To address these challenges, several port projects are underway to accommodate the manufacturing, construction, assembly, and operations and maintenance of offshore wind turbines. This work is driven by industry demand, state government commitments to purchase wind energy, and the pending federal approval of the first major offshore wind project, Vineyard Wind. Port projects are proposed or currently underway in Massachusetts, Rhode Island, Connecticut, New York, New Jersey, and Maryland.
The geotechnical challenges of constructing large port facilities
Port facility construction presents distinct geotechnical engineering challenges. Near-shore facilities are often located in areas with thick sediments that have built up over decades, centuries, and even tens of thousands of years. These loose, soft, and usually organic sediments tend to be impacted by industrial activities that require proper handling and disposal, which can potentially disrupt your schedule or budget.
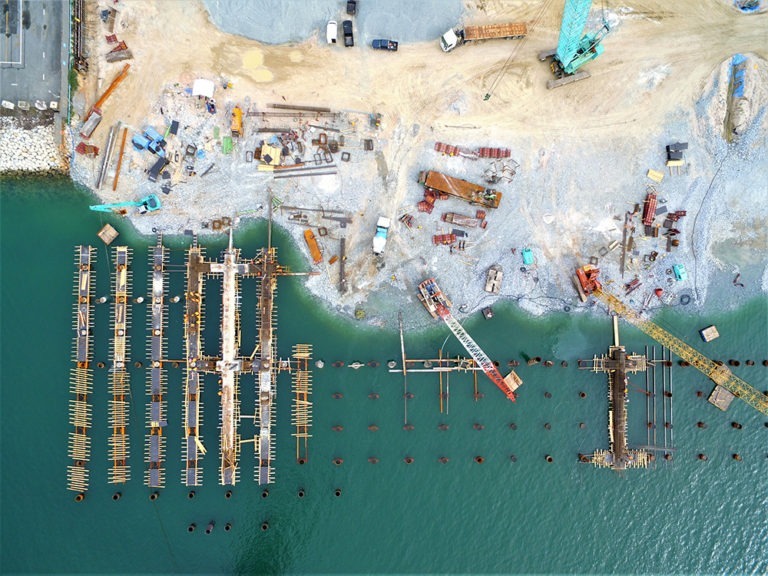
When dredging sediments, you’ll need a sound slope stability assessment that considers the weight and strength of the materials in the area. Thicknesses vary from a thin veneer in areas that have faced ongoing erosion to over 100 ft thick where deposits are undisturbed in tidal flats, large river confluences, and deltas. These sediments’ consistency, ranging from “mayonnaise to pudding to peanut butter,” commonly require special in-place strength testing that will give you the data needed to choose the right foundation solution.
If the most suitable deep foundation system is not used, building on these sediments can be highly difficult and expensive. Bearing piles for port structures are typically complex and can include heavy-duty pipe piles, drilled shafts, pre-cast concrete piles of various shapes, and large diameter pre-stressed cylindrical piles. Your geotechnical team needs to consider the various forces impacting the capacity of the piling/pier system, including the substrate.
You can see the importance of having a thorough understanding of the complex soil-structure interaction of these systems. Selecting the right bearing pile/pier system can mean the difference between financial success and project stability, or cost overruns during construction and significant foundation problems that may arise later. Also, if your geotechnical team can eliminate unnecessary pilings or pier units, it can save you hundreds of thousands of dollars.
A final geotechnical challenge is selecting the proper port water retainment system. Your team needs to consider the area’s geometric constraints and the geologic conditions. Again, it is critical for your engineering team to properly investigate and interpret the subsurface conditions to design an optimal waterfront retainment system. Your choices for the port bulkhead system are varied—from conventional steel sheeting pile walls, to combination walls, king-pile walls, cellular cofferdams, diaphragm walls, and gravity walls. These systems can be freestanding and cantilevered or tied-back with deadmen and/or soil/rock anchors. The engineers need to know the best solution for the conditions.
Your field studies are critical to understand the complete soil structure picture essential to ensure a successful project design. In general, sampling over water is more time-consuming, may be delayed by weather and other logistical challenges, and is more expensive to implement than land-based sampling. Thus, geotechnical engineering and geologist teams need to thoroughly plan field exploration programs prior to implementation. These studies rely on the unique tools in the geotechnical engineer’s arsenal of investigative methods.
When working with our clients, we use on-the-water standard penetration testing and cone penetrometer testing with seismic cones as the backbone for our field studies. When it is beneficial, we have also added unique tools such as in-situ vane shear testing, packer testing, optical acoustical televiewer, vibracores, pressure meter testing, seismic refraction surveys, and SPSS surveys.

Haley & Aldrich engineers have implemented extensive field studies for the design and construction of port facilities along the U.S. eastern seaboard for the USS Constitution new berthing structure, the super flood basin at Portsmouth Naval Shipyard, and the new flood containment structure at Norfolk Naval Shipyard. We have also completed field studies and design for an offshore wind staging facility in New London, Connecticut. Are you planning to prepare a port or harbor facility for offshore windfarm construction? Contact us to discuss your geotechnical engineering challenges.
Read more blog posts on offshore wind construction and engineering:
Published: 1/6/2021
- Energy
- Renewable energy
- Government infrastructure
- Ports, harbors, and coastal Infrastructure
- Contaminated site management
- Sediments
- Foundation design
- Geotechnical instrumentation and monitoring
- Geotechnical engineering
Author
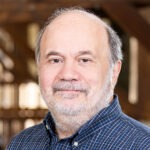
Program Manager, Geotechnical Engineering