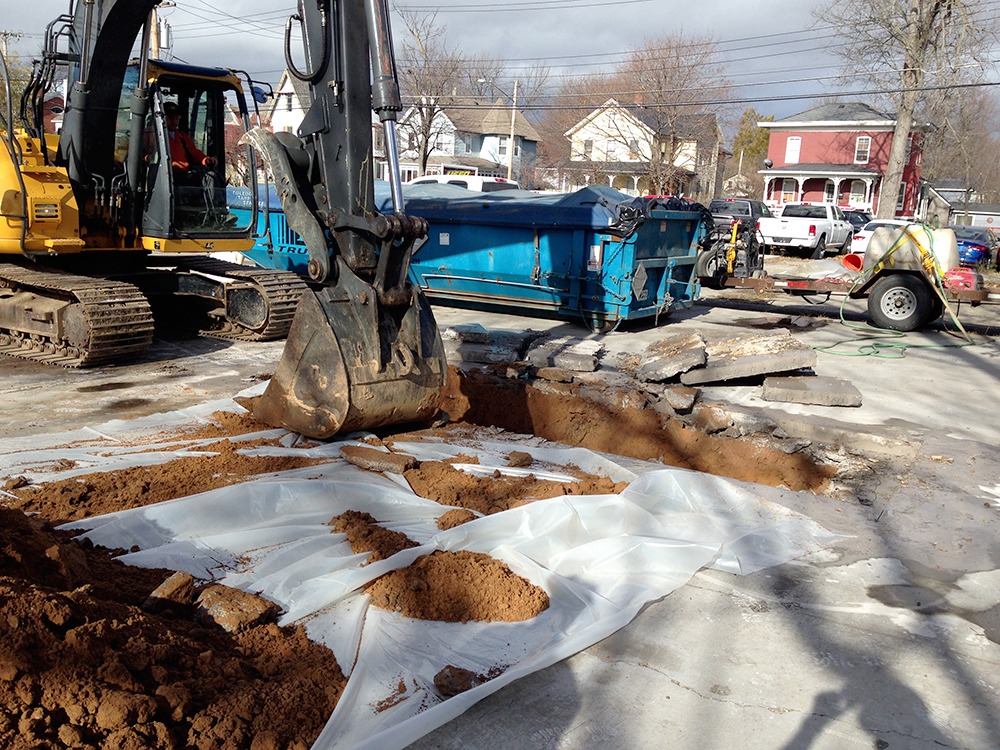
Manufactured gas plants
Our plan shrinks remediation scope, cuts costs for former gas plant site
Summary
- Haley & Aldrich helped a utility company come up with a remediation plan for a former manufactured gas plant (MPG) site.
- Our team used a cost-effective testing approach to find out the extent of contamination resulting from MGP operations — and therefore, what our client was responsible for remediating — vs. the extent from the surrounding environment.
- Our findings saved the client significant costs by revealing that the remediation could be less extensive than originally expected. We also secured regulatory approval for the remediation plan.
Client challenge
The project required regulatory and remediation expertise, in addition to the sensitivity needed to ensure that residents, a retail business, and river activity were not disturbed during investigation and remediation activities. The client had to determine which coal gasification byproducts came from the MGP site and required remediation, and what byproducts were typical of an urban setting that historically used coal for heating and manufacturing. Determining what contamination was related to MGP operations and what was considered ambient conditions was a challenge.
A utility company needed to investigate and remediate a former MGP site in accordance with a multisite consent order from the New York State Department of Environmental Conservation (NYSDEC). The client had to determine the extent of the MGP-related subsurface impacts at the site, located adjacent to a river and canal. This included investigating potential impacts to an on-site retail business, adjacent residential properties, and the recreationally active river and canal — all while limiting disruptions and meeting regulatory demands.
The client turned to Haley & Aldrich for not only our deep experience with remediating MGP sites, but also our sensitivity and effectiveness in working with the community and regulators to achieve site closure.
Our approach
Determining the extent of required remediation both on land and in the river took a high level of MGP site investigation and remediation expertise. However, our community relations skills were just as important. Our first goal was to make things easy for the public, including addressing noise, dust, and safety concerns. We communicated with residents and the retail business owner, ensuring our work didn’t interrupt daily life and business activities.
Haley & Aldrich had no subsurface site information; therefore, we needed to perform soil boring and test pits on the nearby residential properties. Results showed the extent of MGP-related byproducts was limited and Haley & Aldrich was able to distinguish these impacts from typical urban fill found throughout the area. Our team also worked with the retail business owner to safely conduct a soil vapor intrusion (SVI) investigation, which did not indicate any impact to indoor air quality. Our team collaborated with the owner to identify an approach that would keep the business operational and avoid impacts to employees and customers.
We also completed a sediment investigation of the river and canal to identify coal tar impacts. To control costs of necessary but potentially budget-breaking investigative borings on the river, we coordinated closely with our in-house sediment experts and developed an adaptive work plan, completing work in one mobilization. These efficiency measures provided a double benefit: avoiding additional permits and remobilization efforts for new sampling while gathering a complete snapshot of sediment conditions.
“Working smart to keep down costs while also meeting stringent state standards was crucial, but negotiating with the on-site business owner and communicating with residents was just as important.”
Douglas Allen, Haley & Aldrich
We were able to demonstrate that the concentration of polycyclic aromatic hydrocarbons (PAHs) in upstream and downstream sediment were equivalent, limiting the area of sediment that needed to be remediated. Limiting the area of soil removal to the upland portion where the gas plant footprint was, with insitu solidification and soil capping in other portions of the site allowed us to ultimately save our client significant costs in remediation construction and soil disposal. In addition, the remediation contractor provided his input and fine tuned the overall remediation construction approach to streamline moving the site from initial site investigation to remedial design.
NYSDEC approved our remediation plan. Most of all, our client was pleased with how we communicated with regulators, residents, and the retail business while providing technical and regulatory expertise. Following our recommendations, the site was remediated and successfully closed.
Value delivered
- Cleared path for MGP remediation and closure
- Saved significant costs by limiting the scope of remediation
- Communicated with residents to ease minds and avoid community disruption
- Limited the river and canal sediment remediation to a manageable area that was MGP-related
For more information, contact:

Senior Technical Expert