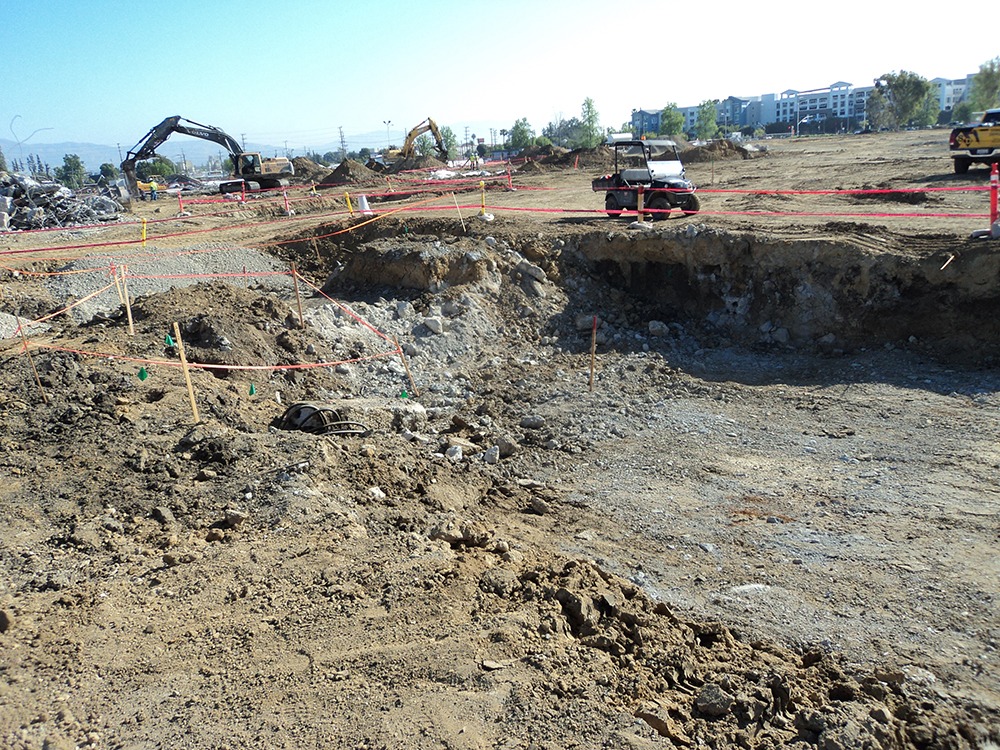
Aerospace
Stakeholders collaborate to create a unified vision, preparing aerospace manufacturer to divest large, environmentally impacted land parcel
$100,000s
saved by our alternate waste management approach for rainwater
$100,000s
saved in handling of PCB-impacted demolition waste
Zero
safety incidents recorded over nearly 10,000 hours worked
Summary
- Haley & Aldrich’s remediation team helped our aerospace manufacturing client quickly divest a 47-acre property with soil and groundwater contamination.
- We successfully remediated soil to meet risk-based residential goals, enabling the client to get the highest sale price for the land.
- The client also saved hundreds of thousands in costs because we proactively identified an alternate waste management approach for rainwater.
- The client’s success was enabled by our ability to identify the best science to address numerous remediation, stakeholder, and regulatory challenges, and to facilitate collaboration.
Client challenge
An aerospace manufacturer sought to divest a 47-acre property with soil and groundwater contamination from trichloroethylene (TCE) and other chemicals of concern. To prepare the land for divestment quickly, the company’s remediation and real estate teams needed to understand one another’s goals and reach agreement on a path forward. In addition, the manufacturer needed the soil to be remediated to residential risk-based soil remediation goals (SRGs) to garner the highest sale price. Developing and executing on a cohesive plan quickly was further complicated by public agency regulations with tight deadlines, and a vigilant community.
The company engaged Haley & Aldrich to identify the best science to address numerous remediation, stakeholder, and regulatory challenges, and to bring together the disparate parties so they could reduce the company’s liabilities while protecting the environment and community.
Our approach
Haley & Aldrich staff worked with the remediation, oversight agencies, and real estate stakeholders to create a shared understanding of issues, constraints, timelines, and risks. We identified potential future regulatory, remediation, and schedule impacts, and created supporting risk-based mitigation plans to get ahead of issues that could arise.
With all stakeholders we defined an end goal and supporting plan with which all parties were aligned. To remediate and sell the property for residential reuse, we included elements in the plan to ensure that the site remained under a voluntary cleanup action throughout the project. We also secured residential risk-based SRGs and an Environmental Land Use Covenant (ELUC) to address potential exposure risks from VOCs in soil gas and groundwater.
We also recommended and led an investigation of the large factory floor for polychlorinated biphenyls (PCB) contamination, which the client believed was not a contaminant of concern at the site prior to demolition. We identified best management practices for the PCB-impacted materials and ultimately saved the client hundreds of thousands of dollars and significant time.
Value delivered
- Remediated soil to risk-based residential goals
- Saved hundreds of thousands of dollars by proactively identifying an alternate waste management approach for rainwater
- Recorded zero safety incidents, OSHA recordables, and time lost to incidents in nearly 10,000 hours worked
- Saved client hundreds of thousands of dollars more in PCB-impacted building demolition waste
For more information, contact:
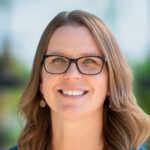
Senior Project Manager