Research has indicated that some of the most useful features in today’s textiles — from stain-proofing in carpets to rainproofing in jackets — may be harmful during three different phases in their lifecycles: manufacturing, use, and disposal. Textile manufacturers should be aware of the risks so they can be prepared for regulatory actions.
Per- and polyfluoroalkyl substances (PFAS) are a group of several thousand individual synthetic, fluorinated organic compounds. Due to their unique physical and chemical properties, PFAS have been widely used in everything from consumer products such as textiles (as well as paper and non-stick cookware) to industrial applications such as firefighting foams and fume suppressants in chrome plating processes.
Increasing evidence shows that PFAS may cause harmful impacts to human health and the environment. As a result, U.S. federal and state agencies have started publishing stringent regulatory and guidance values for PFAS in drinking water, groundwater, soil, and air. The European Union published regulations to limit the use of perfluorooctanoic acid (PFOA) and perfluorooctane sulfonate (PFOS) at 1 microgram per square meter (µg/m2) on textiles and other coated products.
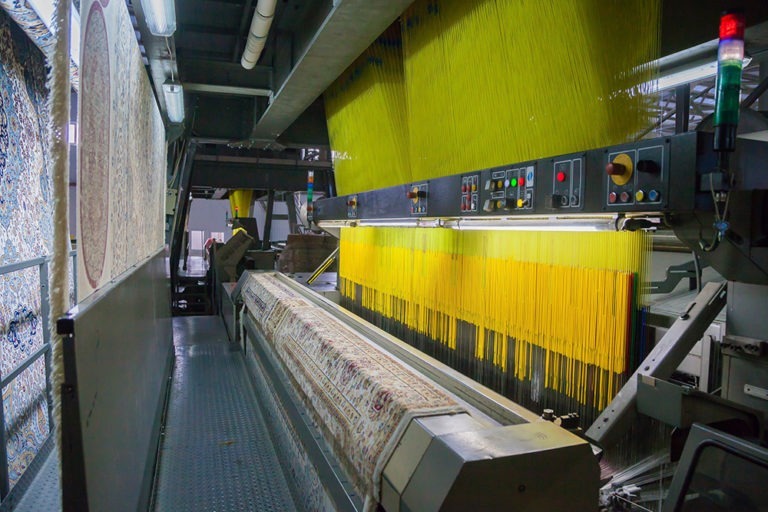
Below, we outline why manufacturers use PFAS in textiles and the potential for PFAS release to the environment during the three phases of the textile lifecycle. On February 28, 2020, the California Department of Toxic Substances Control (DTSC) proposed regulations listing carpets and rugs containing PFAS as a Priority Product, a consumer product identified by DTSC that contains one or more chemicals with a hazard trait. It’s important for textile manufacturers to understand where PFAS releases will appear in their products’ lifecycle, as well as the potential impact on human health and the environment, so they can be ready to respond to applicable regulations.
PFAS use in textiles
PFAS exhibit oleophobic and hydrophobic properties, meaning that they repel oil and water, respectively. The repellents extend the lifetime of a product and, by lowering the fiber’s surface energy, impart water, oil, soil, and stain repellency to textiles.
Fluorochemicals are the most commonly used repellents in the textile industry due to their ability to repel oil and dirt. These repellents are mainly made of fluorinated polymers, which are applied as a thin film on the fabric surface, usually in combination with other finishing auxiliaries. Residuals and impurities of the fluorinated polymers may be released directly from the products into the environment through washing and/or volatilization. Additionally, the polymers can degrade under environmentally relevant conditions, resulting in the release of fluorinated alcohols. Once in the environment, fluorinated alcohols can break down into the PFAS perfluoroalkyl carboxylic acids (PFCAs) and perfluoroalkyl sulfonic acids (PFSAs), which have high persistence and tend to bioaccumulate.
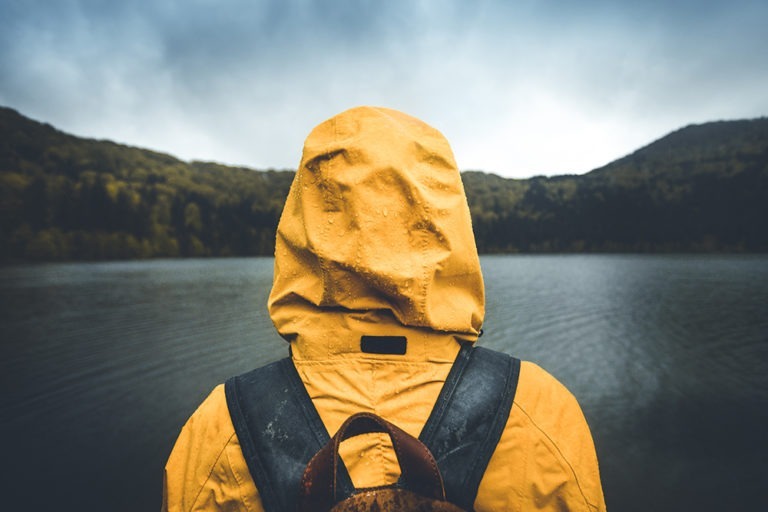
Several studies of PFAS use in textiles have been reported in the literature. Santen reported that PFAS were detected in samples obtained from all 14 rain jackets and rain pants manufactured by major brands, with elevated levels of PFCAs and fluorotelomer alcohols (FTOHs). Kotthoff et al. investigated PFAS in consumer products across 115 random samples including textiles (outdoor materials) and identified a high concentration of PFAS in outdoor textiles (up to 19 µg/m2 of PFOA). Robel et al. used several different analytical methods to quantify volatile and ionic PFAS, precursor PFAS, and total fluorine on nine textile samples (jackets, children’s fabrics, hats, pillowcases, and office upholstery).
The results show PFAS in textile samples remained on the surface after extraction, which indicates that PFAS are likely to continue to wash off gradually. The same researchers found that older textiles had a larger faction of extractable PFAS, suggesting that older materials may be a greater potential source of exposure to PFAS than newer ones.
PFAS release from textiles
PFAS can be released from textiles at three different phases of their lifecycle: manufacturing, use, and disposal. The release mechanisms from these stages are summarized below:
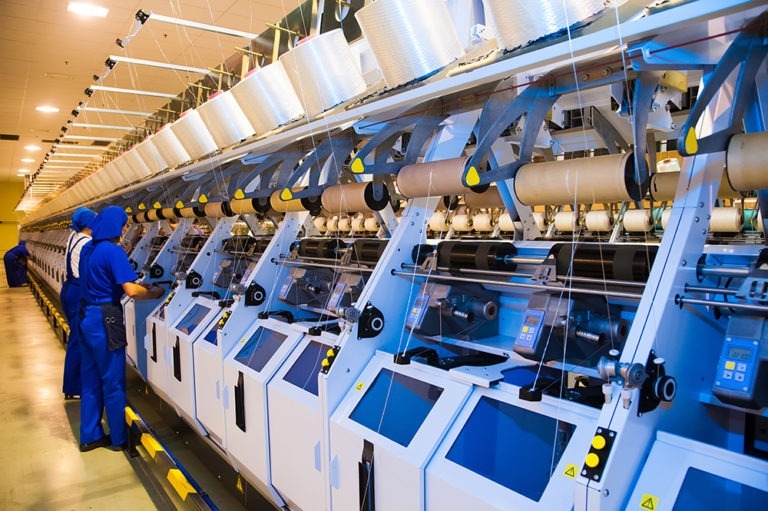
- Textile Manufacturing: The manufacturing of certain high-performance textiles uses many chemical treatment steps that involve PFAS to protect the textiles against water, stain, and oil penetration. Heydebreck reported the presence of PFAS in wastewater, air, airborne particles, and settled dust in a textile manufacturing facility, with long-chain PFAS (such as PFOA, perfluorodecanoic acid [PFDA], and their precursor compounds fluorotelomer alcohols [8:2 FTOH and 10:2 FTOH]) as the dominant compounds in all the tested environmental media.
- Textile use: Most of the repellent-treated cloths undergo reduced repellency during their lifetime. PFAS can be released from clothing through a number of mechanisms including:
- the evaporation of volatile PFAS as a residual from the fabric;
- the wash-out of water-soluble residuals like PFOA;
- the loss of particles and fiber fragments containing fluorinated polymers by abrasion;
- the chemical breakdown of fluorinated polymers during laundering and the loss of fiber fragments during the washing process into the effluent;
- the release of fiber fragments via the wastewater treatment plant and the further transformation of the precursor compounds; and
- the breaking of the carbon-oxygen bond of the fluorinated side-chain.
- Textile disposal: In the United States, most textiles (e.g., carpet and clothing) are disposed in landfills at the end of their useful lives. A product disposed in a U.S. landfill will be exposed to both physical leaching through infiltration of precipitation and to anaerobic biodegradation. Leachate is the contaminated water that infiltrates through the waste mass in landfills. A recent study evaluated PFAS release in the aqueous phase of anaerobic model landfill reactors filled with clothing or carpet. Up to 70 PFAS compounds were measured in the model’s landfill leachate.
Modern textile features such as stain resistance and waterproofing are useful for consumers, but the PFAS that make them possible may pose risks to human health and the environment. Manufacturers should be aware of the potential risks and prepare for new regulations that federal and state agencies are now developing. Please contact either of us to discuss your textile manufacturing challenges or with any other PFAS-related questions.
Published: 3/16/2021
Authors
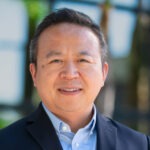
Principal Consultant, Applied Research Leader
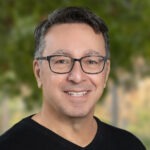
Principal Consultant