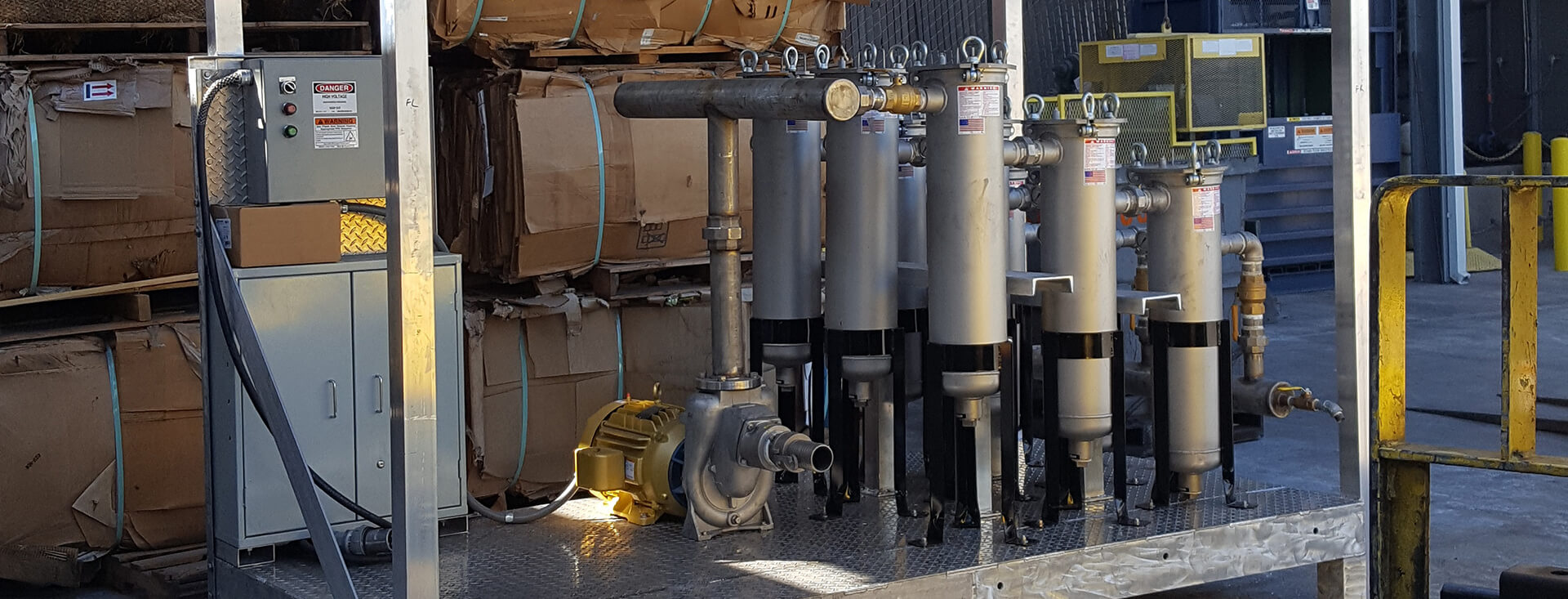
Manufacturing
Manufacturer maintains compliance and avoids production disruptions with updated stormwater solutions
$20,000
saved annually on system maintenance
$100,000
saved with custom stormwater management system
Summary
- Haley & Aldrich’s stormwater experts helped an aluminum manufacturer in California understand and comply with stricter state permitting requirements.
- Our team helped identify the sources of pollutants at the client’s facility and determine how they were getting into stormwater, then planned solutions.
- The client saved hundreds of thousands in purchase and annual maintenance costs by working with us to develop a bespoke filtration system that would keep pollutants out of water runoff.
- Our team worked with staff on the manufacturing floor to find solutions, working to make sure they could meaningfully integrate best practices into their work.
Client challenge
California regulators reissued the state’s stormwater Industrial General Permit, adding new industry-specific effluent benchmarks for compliance. Our aluminum extruding and finishing client had four Southern California facilities affected by the new permitting requirements. Metals manufacturers in California have generally set up their facilities with a large proportion of outdoor space reserved for storing raw materials and waste generated by their operations. This practice meant that our client’s materials were outside, where they could be blown around by the wind or disturbed by staff and equipment such as forklifts, which had to navigate around them. Once the materials — many of which are relatively small — spread around their facility, they more easily ended up in stormwater, leading to exceedances under the new, more stringent permit requirements.
Like others in the industry, our client operates their business on slim margins, and a new stormwater treatment system, likely to cost half a million dollars, would be unaffordable. We had earned their trust years earlier helping them avoid a Clean Water Act lawsuit at one of their facilities by working with the community and alleviating their concerns. Once again, they called on Haley & Aldrich’s stormwater experts to interpret and help them comply with the new regulations and address any exceedances.
Our approach
Prior to the effective date of the new permit and implementation of the effluent benchmarks, Haley & Aldrich assisted our client in reviewing samples collected under the old permitting requirements. We compared those results with the new permit’s effluent benchmark requirements to determine how close the facilities would be to meeting the new limits.
After establishing a baseline, because of the nature of their business, as expected, our client discovered aluminum exceedances at all four of their facilities. In addition to aluminum, each facility had other parameters that exceeded benchmarks. The new permit also required minimum Best Management Practices (BMPs) as well as Exceedance Response Actions if effluent concentrations exceeded benchmarks.
So, we worked with our client to initiate housekeeping processes to keep the metals from impacting stormwater and updated their Stormwater Pollution Prevention Plans. We made improvements to sweeping methods, scrap storage, yard repairs, inspection zones, and personnel training. Many of these additional BMPs proved effective. Effluent sampled following their implementation met the benchmark limits. For three of the four facilities, no additional improvements were needed.
However, even after implementing new BMPs — including storing waste under cover — our client’s Riverside recycling yard and foundry continued to exceed the benchmark limit for aluminum. Our client was determined to find a permanent solution for filtering the pollutants.
Working in tandem with the client’s on-site environmental manager, we researched conventional stormwater filter systems. The systems that could treat aluminum had a large footprint as well as significant operation and maintenance costs and required a maintenance contract. Available stormwater treatment systems with appropriate treatment capability cost over $100,000 for the initial capital investment with an additional annual cost between $10,000 and $30,000.
In addition to the size and cost of the equipment, the systems lacked the flexibility to manage the stormwater variability, resulting in changes in operations. During certain periods, the facility stored large volumes of scrap that would be exposed to stormwater. To overcome the financial and technical obstacles, we first evaluated the methodology and technology used at the facility’s existing wastewater treatment system. We then combined that technology with the technology used by conventional stormwater treatment systems to create a customized stormwater treatment train.
The custom design allowed our client to modify and troubleshoot the system as needed — an additional advantage. Costs for the client-designed system were approximately $30,000 with annual maintenance and modifications of just $5,000 per year. The new system worked, and concentrations of aluminum returned to baseline levels below the benchmark limit.
Value delivered
- Identified where pollutants may originate and brainstormed ideas with client’s environmental manager for improving their BMPs.
- Saved manufacturer about $100,000 in purchase costs and an additional $20,000 in annual maintenance costs by co-developing customized flexible solutions.
- Avoided disrupting operations at the facility by recommending stormwater treatment systems based on current operational practices.
- Involved personnel on the manufacturing floor to resolve their environmental challenges, which made them more likely to adopt best practices going forward.
- Co-presented our accomplishments with the client’s environmental manager at the California Stormwater Quality Association conference.
For more information, contact:
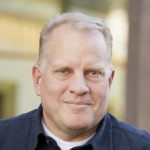
Service Leader, Water Resources