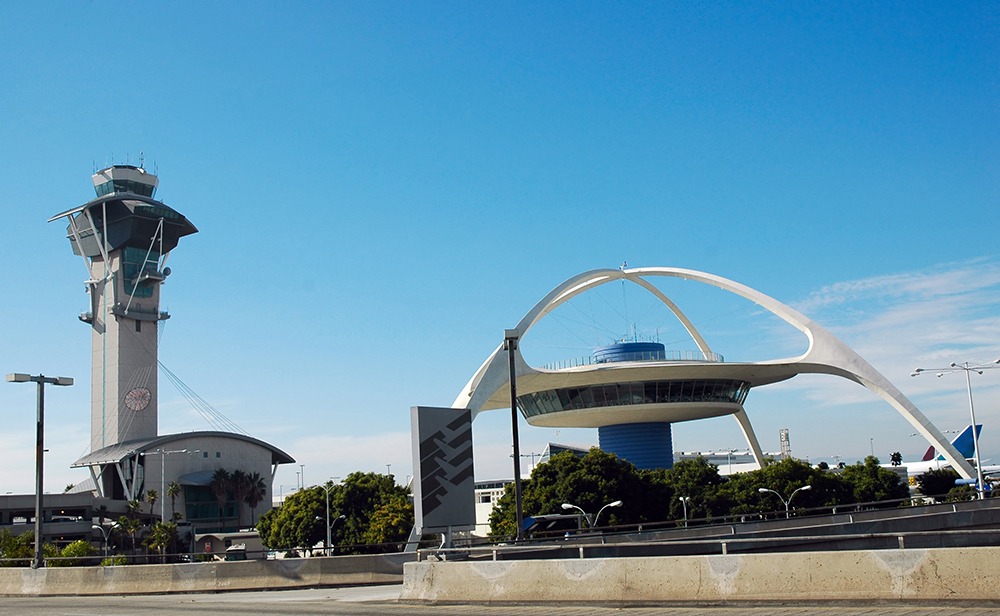
Aerospace
Innovative, risk-based plan for remediating jet fuel plume saves airline millions of dollars
$1 million+
gallons of jet fuel recovered and recycled
$5 million
saved in operations, maintenance, and monitoring costs
$300 million
saved in remediation costs
Summary
- Haley & Aldrich helped a major airline overcome regulatory scrutiny and escalating costs as it remediated a 2 million-gallon jet fuel plume.
- We devised a risk-based closure plan that secured our client the confidence of regulators and LAX, while saving millions of dollars in operating costs.
- By modifying the existing recovery system and advocating for natural attenuation instead of much more expensive enhanced recovery options, we saved the airline $300 million while also incorporating significant sustainability elements.
Client challenge
Our airline client faced regulatory scrutiny and escalating costs in remediating a 2 million-gallon jet fuel plume under their maintenance facility and taxiways at Los Angeles International Airport (LAX). Another consultant had recently installed a multimillion-dollar recovery system. However, the local water table had been rising, submerging the jet fuel, and the original recovery system by design could not extract the fuel both underneath and on top of the water table. This attracted the attention of the Los Angeles Regional Water Quality Control Board, who wanted all the contamination addressed. The airline sought Haley & Aldrich for our reputation for infusing science with client advocacy and contracted us to find a cost-effective path forward for closing the site that would satisfy our client, LAX, and the water board.
Our approach
Haley & Aldrich devised and advocated for a risk-based closure plan that addressed the jet fuel plume and secured our client the confidence of regulators and LAX, the nation’s third-busiest airport. By modifying the existing recovery system and advocating for natural attenuation instead of inordinately more expensive enhanced recovery options, we saved the airline $300 million.
We also improved the system’s performance and reliability enough for our client to recover and recycle more than 1 million gallons of jet fuel. And we made our case for natural attenuation to regulators by adopting a tool created by academics that measures carbon dioxide flux over time to calculate the rate at which jet fuel naturally degrades. On the business side, to gain control of the recovery project’s budget, we applied our experience with similar clients and projects to quickly identify process and system inefficiencies.
Value delivered
- Negotiated a risk-based closure plan that saved the client $5 million in operations, maintenance, and monitoring costs
- Saved the client $300 million by advocating for more cost-effective, risk-based remediation methods
- Reduced costs while incorporating significant sustainability elements
- Incorporated Lean processes and thinking throughout the project for holistic savings and improvement
- Negotiated an exit strategy that met all stakeholders’ needs
For more information, contact:
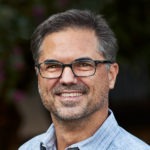
Technical Expert, Hydrogeology