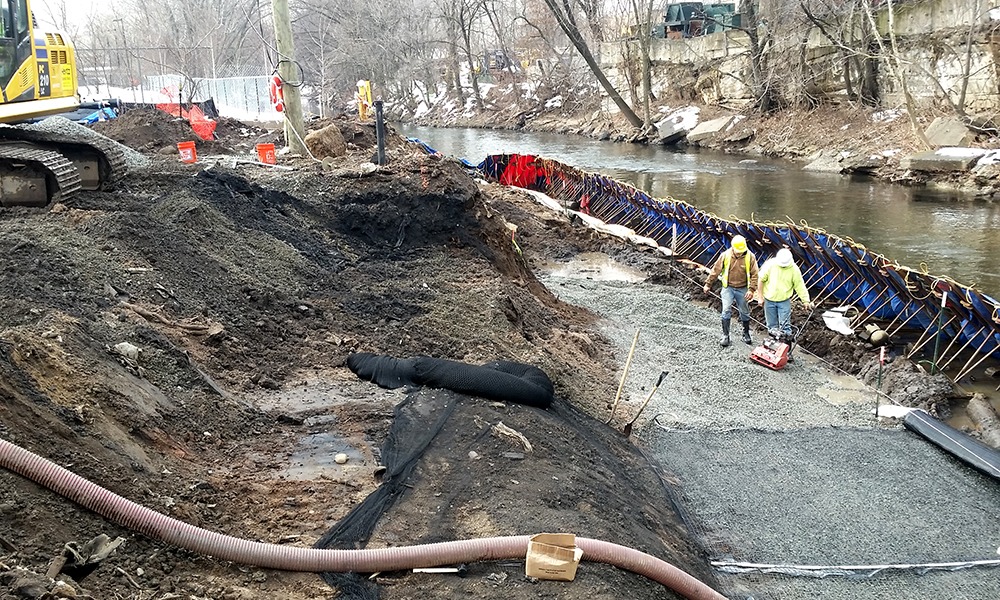
Aerospace
Over three decades, we help client successfully navigate complex remediation project
80%
amount we reduced excavation area through innovative treatment tech
$8.6 million
saved in project lifecycle remediation costs
Summary
- An aerospace company needed to remediate the severely contaminated site of a chemical manufacturing facility — a complex, three-decade project.
- The client partnered with Haley & Aldrich from the very beginning because of our strategic approach to remediation and our technology and regulatory experience.
- We drew on our technical expertise to develop an environmentally responsible, efficient approach to remediating the soil and groundwater.
- We also helped manage U.S. Securities and Exchange Commission (SEC) reporting obligations and adapted the remediation plan to changing regulatory requirements and our client’s goals.
- The property is now a thriving retail center.
Client challenge
An aerospace client sought to achieve site closure under a very stringent and prescriptive regulatory program for a former chemical manufacturing facility. The severely contaminated site had been used to store, handle, and blend hundreds of chemicals during its century-long industrial history. Logistical hurdles including its riverside, in-town location and ongoing manufacturing operations created additional complexity. Over the course of three decades, our client was responsible for site investigation and remediation mandated by an administrative consent order while a series of complicating factors unfolded.
One such factor was the threat of the township’s taking over the site under eminent domain so it could be redeveloped. In this scenario, the site’s redeveloper would be responsible for remediation and was likely to implement an excavation-only approach that involved digging out and moving the contamination to a landfill or incinerator. This approach would not only add $9 million in costs, but posed liability concerns for the client, as well as safety concerns for the community, with hundreds of trucks carrying contaminated soil past a nearby school. The client was also concerned that the excavation approach would not address the significant groundwater contamination, leaving the company open to further regulatory action.
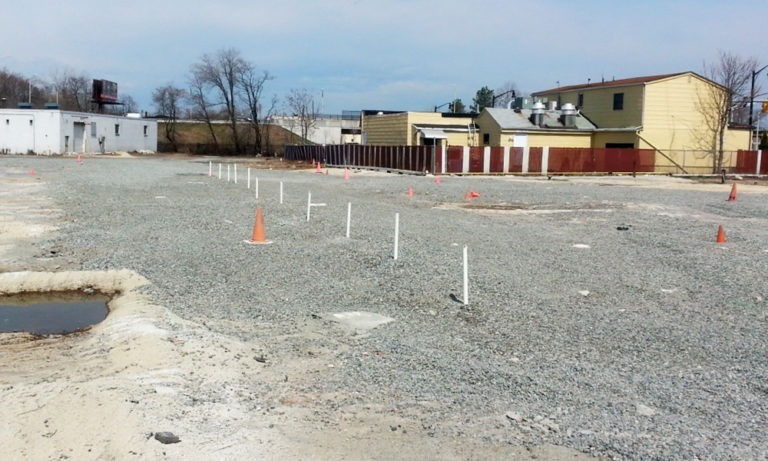
The client decided to pursue an aggressive remedial strategy to prepare the site for redevelopment while keeping control of the remediation. To finalize the property sale to the developer, our client needed to complete all remaining active remediation, implement administrative and engineering controls, and procure permits for long-term Monitored Natural Attenuation (MNA) within just six months.
The client engaged Haley & Aldrich as its partner from the very beginning due to our strategic approach to remediating complex sites, experience with innovative technologies, and our deep knowledge of state regulations.
Our approach
Given the site complexity and potential threat to the river, we employed an innovative and adaptive management approach to the overall investigation and remediation strategy for the site. The regulatory agency approved our proposed approach to sequence the implementation of treatment technologies for different site areas of concern. This helped the client mitigate and control potential threats to the river while moving forward with investigating and remediation planning for other areas of the site. Although the regulations seemed inflexible, we used our knowledge of their provisions to negotiate an end to active remediation when our client achieved certain technology milestones.
Program management success
- During this decades-long project, we adapted to our client’s evolving needs as management reporting, financial, accounting, and auditing requirements changed.
- We helped the client manage SEC reporting obligations for environmental liabilities by understanding the reporting rules and utilizing probabilistic cost estimating.
- To align with our client’s goals and vision for the site, we adapted the pacing and implementation of activities.
- We utilized Lean tools for project planning and management, enabling us to deeply understand our client’s values and desired outcomes and align our project team accordingly.
Another significant component of our strategy was to remediate soil and groundwater jointly, contrary to the regulatory agency’s preference to excavate contaminated soil first and then address groundwater. We began by implementing dual-phase extraction (DPE) technology to remove significant amounts of contaminants. Our use of innovative treatment technologies, including adsorbent resin, allowed us to procure a permit for discharge of treated groundwater directly to the river, a much less-expensive option. Where there were still elevated concentrations of contaminants, we performed thermal remediation on soil and groundwater as a combined media. This reduced the areas requiring excavation by 80%.
Remediation innovation
We designed and oversaw the installation of sheet piles as a source-control measure. We also used the sheet piles for a sequenced and effective implementation of DPE and thermal remediation technologies for significant mass removal including non-aqueous phase liquids (free product).
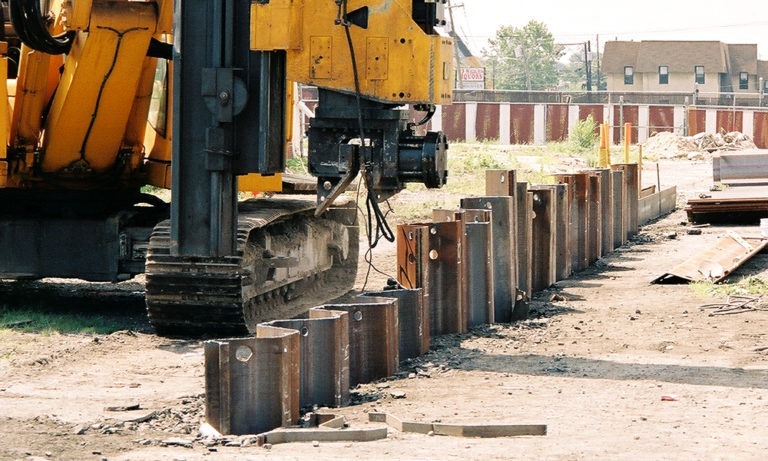
The next step in the active remediation was “polishing” using various bioremediation and oxidation technologies. We then excavated areas with polychlorinated biphenyls (PCBs) over the U.S. Environmental Protection Agency’s standard. Finally, we put administrative and engineering controls in place and procured an MNA permit from the regulatory agency for the property sale to move forward. Due to our planned optimal sequencing of technologies, we were able to complete site remediation within our client’s accelerated, six-month timeframe for the property sale.
We worked strategically and collaboratively with the client as their trusted advisor to help achieve their vision for the site, even with changing goals and conditions. The results speak for themselves: Our client saved millions of dollars and this previously contaminated site has been adapted to beneficial use and redeveloped into a community asset as a thriving retail center.
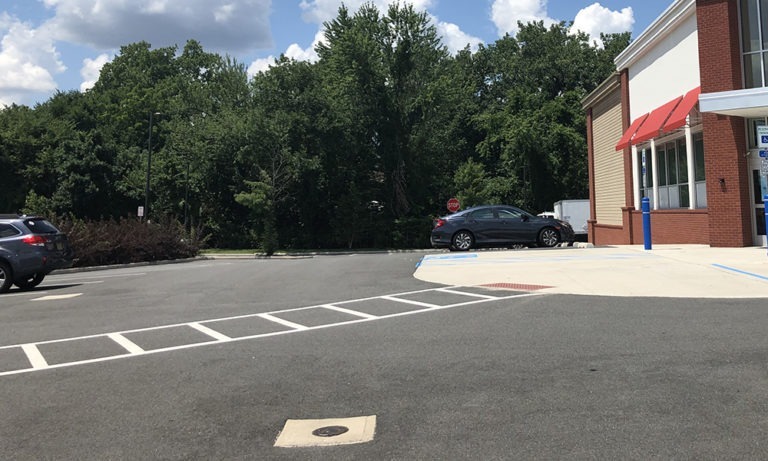
Value delivered
- Adapted remedial strategy and execution to changing regulatory requirements and client management’s goals
- Achieved regulatory closure on an expedited six-month schedule for property sale
- Delivered remediated property for beneficial reuse as part of the township’s redevelopment plan
- Saved the client $8.6 million in project lifecycle remediation costs
“I’m really proud of Haley & Aldrich’s work on this project. Many firms have the technical capabilities to effectively remediate sites, but the success of this project was in combining the technical capabilities with strategic thinking and innovation to meet the client’s goals. We used our regulatory knowledge to ensure our client wasn’t forced to remediate this site unnecessarily and indefinitely.”
Sunila Gupta, Haley & Aldrich
For more information, contact:
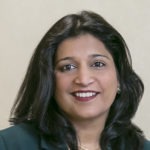
Program Manager