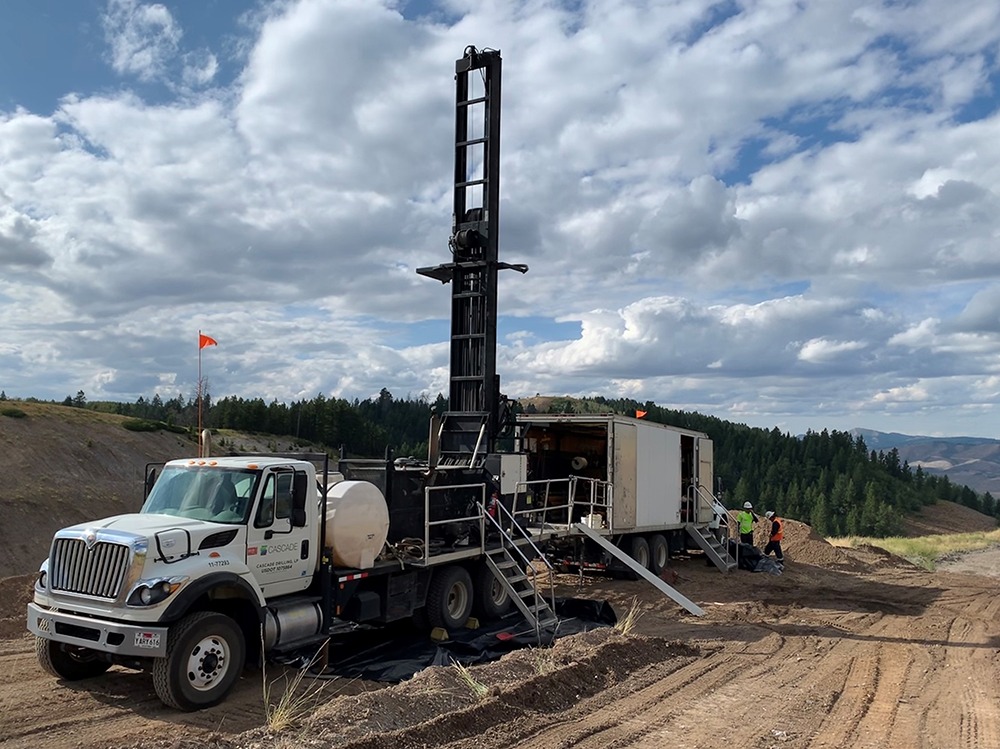
Industrial Minerals
Client safely develops phosphate fields with Haley & Aldrich’s drilling project management expertise
Zero injuries
after 40,000 work hours
2 mines
developed because of our phosphate samples
Summary
- A fertilizer manufacturer was looking to explore the economic viability of a phosphate field in southeastern Idaho.
- The nearly $2 million initiative required navigating a tight timeline and complex wildlife regulations. And with a remote site and long workdays, safety was a major concern.
- Haley & Aldrich developed a comprehensive standard operating procedure that detailed how the team would build the roads and drill pads at all drill locations, as well as how workers and equipment would operate — all crucial to safety.
- We also outlined how we would protect wildlife and ensure no sediment or drilling fluid flowed into waterways.
- Ultimately, we provided the client with representative phosphate samples that led to the development of two mines.
Client challenge
A phosphatic fertilizer manufacturer was looking to explore the economic viability of a phosphate field in southeastern Idaho. The nearly $2 million initiative would include an extensive drilling program of more than 38,000 feet of exploratory borings at 109 locations while balancing seasonal restrictions and wildlife regulations over two seasons. This made project planning very complex, including permitting and monitoring, precise timber removal, building roads and drill pads at each site, and operating five drilling rigs. All areas that would be explored had to be reclaimed under strict regulatory procedures to promote revegetation and habitat restoration. Protecting soil and water quality for nesting birds and other wildlife was also a top priority.
The remote location, more than 40 miles away from the closest town, presented unique logistical problems, including no Wi-Fi or cellular service and difficult terrain to navigate safely. The site location not only made safety a major concern, with the nearest hospital more than an hour away, but average work schedules were 10 days on and four days off with 14-hour days, so project team fatigue was also an issue. The tight timeline, safety conditions, and wildlife regulations complicated the project. Haley & Aldrich’s team had worked with the client before, so they asked for our help to think outside the box to address the complicated challenges associated with this work – and to do so safely.
Our approach
With the project scale and site remoteness, our staff knew we needed to think creatively to develop a safe, realistic drill schedule and operating approach. We tapped into our expertise in Lean to bring all project stakeholders together and create a comprehensive standard operating procedure (SOP). The document detailed how the team would build the roads and drill pads at all drill locations, as well as how the 30 workers, five rigs, and 15 vehicles would operate and move between each site – crucial to worker safety. The SOP also outlined how we would reclaim each drill site, protect nesting sites, and ensure no sediment or drilling fluid would flow into waterways while adhering to federal and state regulations.
It was crucial that team members who were not on the site daily, including the client’s executives and investors, were kept abreast of drilling progress and sampling results. To solve the data-sharing issue, we developed an innovative system that involved portable Wi-Fi hotspots. The hotspots gave enough coverage so on-site workers could update progress to an interactive map that everyone – in the field or office – could use for an up-to-date, interactive geographic reference of every step of the drilling process. This helped field staff save time on critical communication while keeping stakeholders abreast of the drilling progress and sampling results.
However, none of the communication efforts would have made a difference if we didn’t find the right workers. Our SOP included standard roles and responsibilities for every project job to help find the right candidate and get buy-in from each project team member. While our core team included experts from all over the country, we still had to hire local workers to complete our team. We engaged with the community and the Department of Labor to ensure we had local, qualified candidates. Additionally, we managed the hiring of local staff and brought them on as Haley & Aldrich team members to relieve the client of all human resources burdens and streamline the hiring process.
Our extensive planning and communication efforts resulted in no injuries, all drilling completed on time, and full environmental compliance. Eventually, the client built out two phosphate mine operations based on our drilling program, resulting in a substantial return on their initial investment.
Value delivered
- Created efficiencies though a SOP so the client could complete all planned drill locations during each season
- Completed 40,000 work hours with zero injuries
- Provided the client with representative phosphate samples that led to the development of two mines
- Ensured the client was compliant with wildlife and environmental regulations
- Hired local staff for the project, alleviating human resources burden for the client while onboarding qualified staff
For more information, contact:
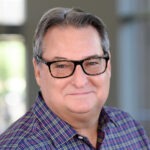
Principal Consultant