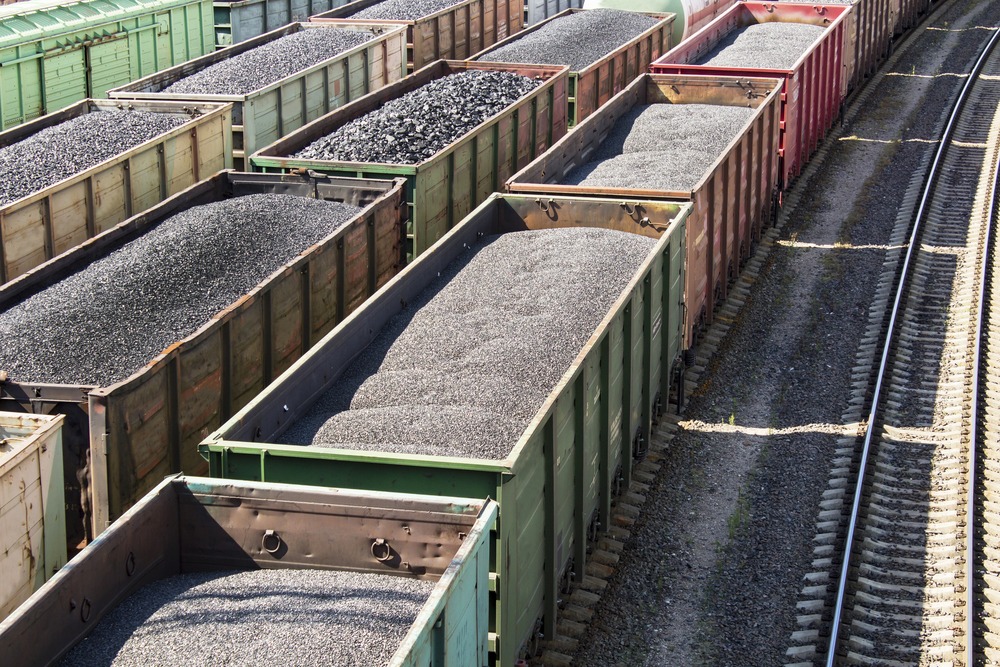
Aggregate and construction materials
We help mining client increase safety and productivity by overcoming procedural and cultural barriers
20%
reduction in safety hazards
Summary
- Haley & Aldrich helped a mining client identify and address risky worker behaviors, drawing on our unusual blend of mining operational knowledge and expertise in management processes and organizational behavior.
- We brought the staff together to identify sources of safety risks, prioritize improvements, and agree on an action plan that gave everyone a sense of ownership.
- Within three months of implementing improvements, our client significantly improved quarry output while reducing its near misses by 20%.
Client challenge
Our client was concerned that many of its rail‐line workers at a massive, high‐volume aggregate quarry were unsafely completing tasks. Rail is the primary means of transporting product out of the quarry, so the potential for a tragedy was high, posing an unacceptable risk to the client and to the workers. While a serious incident had not yet occurred, these workers were not just violating company policies and procedures, they were risking the lives and limbs of all quarry staff — including their own.
Our client needed to quickly identify the underlying cause of the unsafe behaviors: What was happening in the work itself that put so many people at risk? The company turned to Haley & Aldrich for the unusual combination of our knowledge of mining operations and our expertise in management processes and organizational behavior.
Our approach
We knew from experience that those doing the work — in this case, the rail‐line workers — can feel disconnected from management and vice versa. We also knew the best way to understand the situation and expose the reasons for those disconnections was by visiting the quarry to observe what was really happening. So, we gathered all staff together and mapped the steps involved in loading and moving hundreds of rail cars through the quarry.
Through this exercise, we helped the workers collectively identify sources of safety risks in their processes and communicate safety information in English to mainly Spanish‐speaking workers. The workers came to understand their actions as part of a larger system and quickly became part of the solution. Together, with our help, workers and leaders prioritized improvements and agreed on an action plan that gave everyone a sense of ownership.
Value delivered
- Created safer working conditions in the quarry by prioritizing more than 20 improvement ideas that could be implemented in a short period of time
- Within three months of implementing these initial improvements, our client significantly improved quarry output while reducing their near misses by 20%
For more information, contact:
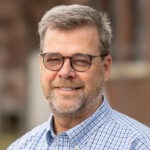
Program Manager, Geology
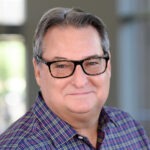
Principal Consultant