
Industrial and manufacturing
Holistic approach and industrial expertise addresses regulatory infraction, saves manufacturer millions
Up to $4 million
saved in engineering and construction costs
Summary
- A manufacturing client faced massive unanticipated costs and, potentially, lost business after receiving a regulatory infraction by an Occupational Safety & Health Administration (OSHA) inspector.
- Through our extensive industrial experience and big-picture thinking, we identified a more appropriate governing criteria, enabling corrective actions to be simpler, faster, and significantly less expensive.
- Our solution satisfied regulators and allowed the manufacturer to continue operations without disruption
Client challenge
A manufacturer that applies powder coating to lawn and garden products was faced with massive unanticipated costs and potential for lost business after being cited for a regulatory infraction by an OSHA inspector. The inspector issued a citation under the OSHA general duty clause, which broadly requires companies to provide a safe work environment.
The citation also specified that the manufacturer needed to comply with National Fire Protection (NFPA) Standard 654, which would require costly modifications to the manufacturer’s facilities’ infrastructure and operations. Although the inspector cited only one plant for combustible dust powder, the manufacturer wanted to get ahead of potential future citations and ensure its nine plants were in compliance. It would have then been necessary for the company to redesign and rebuild powder rooms in nine facilities — which would amount to $2 to $4 million in engineering and construction costs alone.
The client trusted that Haley & Aldrich’s extensive industrial experience, along with our ability to see the big picture and find unconventional solutions, would help them address this potentially costly and complicated challenge.
Our approach
The Haley & Aldrich team knew we needed a solution that would minimize disruption to the company’s critical manufacturing operations and minimize cost. We took an in-depth approach, relying on our many years of industrial expertise and our ability to explore and consider alternate avenues that still met the requirements. We conducted a thorough review of operations, controls, and infrastructure to determine the scope of the issue. Our on-site analysis included observing operations, interviewing employees operating the equipment, reviewing operations manuals, and inspecting the existing controls. We also conducted a regulatory review to identify the most appropriate standard to address the combustible powder concern at the company’s plant.
Through our site visits and regulations review, we recognized that NFPA Standard 654 was not the applicable governing criteria to address the company’s dust powder issue. Instead, we identified NFPA Standard 33 as the appropriate governing criteria, as it specifically addresses powder booths. This was a significant real-world application, enabling corrective actions to be simpler, faster, and significantly less expensive.
An additional part of our strategy was to divide the workspace into three zones, each complying with different aspects of the NFPA Standard. This allowed for varying levels of handling combustible vapors, depending on proximity of the workspace to the powder booth.
Armed with the information and recommendations we provided, the manufacturer presented its case to the OSHA regional director. He agreed with our recommendation to shift compliance to NFPA Standard 33 and with our three-zone approach.
Value delivered
- Saved the client $2 to $4 million in engineering and construction costs alone if they were required to modify nine plants to address the original citation
- Provided the client with the information and recommendations to present their case to the OSHA regional director, preserving the manufacturer’s relationship with OSHA, while also gaining approval of the recommendation
- Identified a solution that satisfied regulators and allowed the manufacturer to continue operations without disruption
For more information, contact:
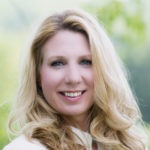
Technical Expert, Health and Safety