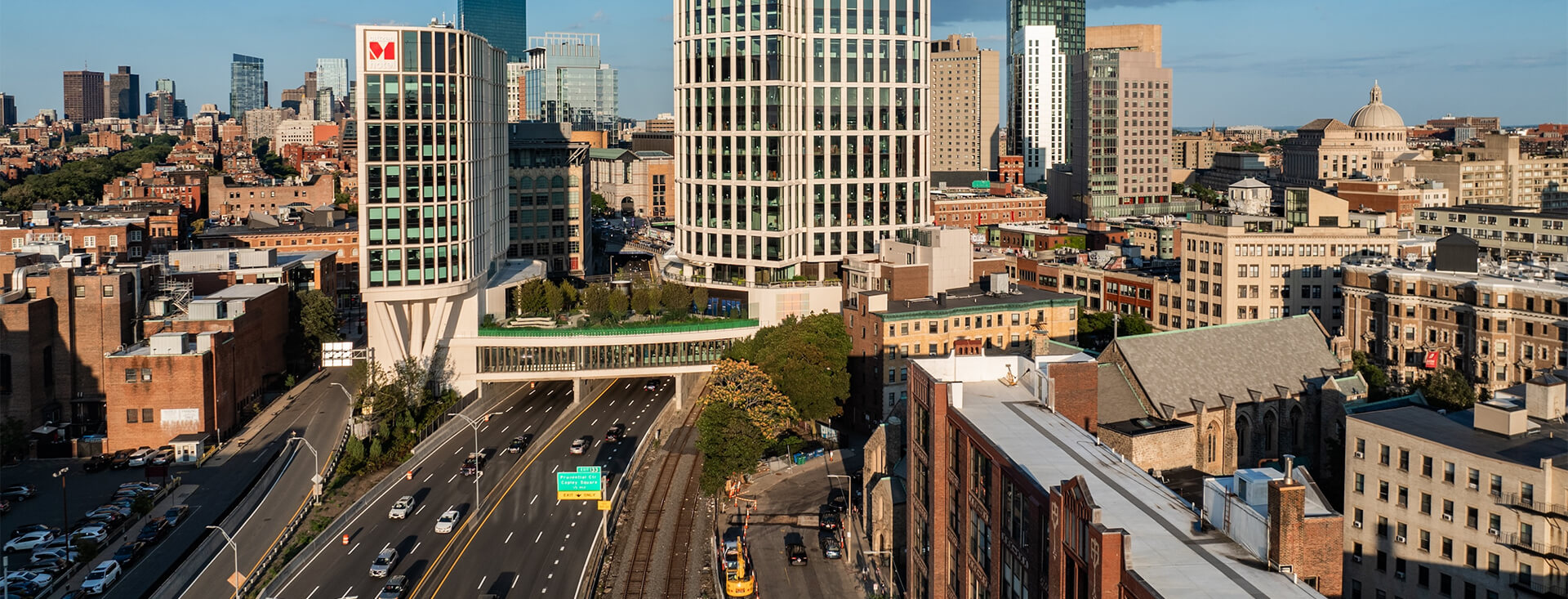
Real Estate Developers
Haley & Aldrich applies every tool in the geotechnical toolbox to deliver project over highway
750+ deep foundation elements
installed across the parcel to ensure stability
First air rights project
completed over I-90 in 40 years
Summary
- Lyrik Back Bay at Air Rights Parcel 12 marks the first completed air rights project over the Massachusetts Turnpike in 40 years.
- To bring the project to fruition, the developer, Samuels & Associates, needed an experienced design and construction team to solve the unique and complex challenges of the project site. They also needed to protect existing infrastructure while working over and alongside an operating highway and a railroad during construction.
- The real estate development firm turned to Haley & Aldrich because of our decades of deep foundation system experience in the city of Boston and our familiarity with the requirements of the relevant public agencies.
- After extensive subsurface investigations, we engineered a unique hybrid foundation system and a support-of-excavation system that met the site constraints and challenges.
- We also developed an extensive monitoring program to minimize disruption to commuters and protect existing infrastructure.
Client challenge
Since the 1980s, Boston has not seen a project like Lyrik at Air Rights Parcel 12. Its completion in 2024 makes it the first successful air rights project over Interstate 90, otherwise known as the Massachusetts Turnpike, in 40 years. Although many other air rights projects had been attempted, they never made it to construction given the many hurdles involved.
Real estate developer Samuels & Associates led the vision for this 1.77-acre Massachusetts Department of Transportation (MassDOT) parcel in Boston’s Back Bay as both an infrastructure and a mixed-use commercial development featuring a 20-story office building, a 13-story hotel, a restaurant, and retail space. The development would cover a gaping hole between neighborhoods created by I-90, provide multimodal transportation improvements, and bring lasting economic benefits to the community.
Most of the construction would take place in the air space over an operating highway and a railroad. Samuels & Associates needed to limit disruptions to highway and railroad commuters and protect MassDOT structures and Massachusetts Bay Transportation Authority (MBTA) track and tunnels — even while working less than 10 feet away in some cases. All this was on a deep foundation system installed in challenging subsurface conditions and limited available space.
Samuels & Associates turned to Haley & Aldrich. With decades of deep foundation experience in the city of Boston plus long working relationships with the design team contractors and our reputation with the public agencies, we were the right geotechnical engineer to overcome these challenges.
Our approach
Haley & Aldrich served as the primary geotechnical and environmental consultant for Lyrik Back Bay. We started with a thorough investigation of the site’s historical use and its subsurface conditions. The project sits partially on land that was created by filling in the tidal flats of the Back Bay in the 1800s to create more developable space for the growing city of Boston. As a result, the upper 25 feet of the land — which consists of fill and soft organic soils — couldn’t support the foundation loads for a project of this size.
In addition, a deep bedrock valley exists below the area that was filled with an up-to-110-foot-thick deposit of soft and compressible clay, referred to locally as Boston Blue Clay. To support the structures that were part of the Lyrik Back Bay project, foundations needed to extend through this soft clay to bear in the bedrock at depths of 125 feet to 175 feet.
Past uses of the site would also impact design and construction. The area has been developed since the late 1800s, with parts of what is now I-90 previously serving as a rail yard and railroad lines. Our site history research and subsurface investigations found structures along Boylston and Newbury streets that had been demolished and buried in place. Also, the MBTA Green Line — one of the oldest subway lines in the country — runs through a tunnel constructed in the 1900s below Newbury Street on the parcel’s north side. Identifying these conditions was critical to mitigate risks, such as delays and cost increases, associated with unknown conditions.
A foundation design that met complex site needs
The investigations revealed that there could be no one-size-fits-all foundation solution. The foundation systems needed to limit noise and vibration; be designed for the poor soil conditions; and surmount the spatial constraints of the narrow turnpike median, the area between the turnpike and the railroad, and the area near other existing structures, such as the MBTA Green Line tunnel.
Our team applied experience and creativity to engineer a unique hybrid deep foundation system. Pile types included high-capacity rock-socketed drilled micropiles, large-diameter rock-socketed drilled shafts, and driven steel H-piles. Combining these systems — which optimized solutions to accommodate the variability in site conditions and addressed the significant complexity of the design and construction of the foundations — was not a typical application. However, our team demonstrated innovative thinking coupled with the design analyses that proved it could be done.
A support-of-excavation system that protected rail lines
Construction of the below-grade parking garage — within 10 feet of active railroad tracks — challenged us to design an innovative hybrid support-of-excavation system. We combined concrete diaphragm (slurry) wall and secant pile wall types, which solved a critical challenge: how to limit movement of the tracks to prevent damaging them during excavation and construction.
For the support-of-excavation wall next to the railroad tracks, we had to keep lateral deflection within less than one inch — an extremely low performance criterion compared to conventional practice. Instrumentation that measured this deflection captured a maximum of approximately one-half inch, which meant our solution exceeded performance expectations.
Part of our support-of-excavation system became permanent. We incorporated the temporary earth support system as the final walls for the below-grade parking garage, a decision partially driven by space restrictions. The secant pile wall not only served as the temporary earth support and permanent foundation wall for the garage, but specific elements also were extended and socketed into bedrock to serve as drilled shaft foundations supporting high building column loads.
Value delivered
- Designed a deep foundation that combined existing technologies in unique ways to address the site’s subsurface conditions and spatial constraints
- Protected existing infrastructure with strategic support-of-excavation design and comprehensive, around-the-clock monitoring that warned of potential impacts of construction activity on surrounding infrastructure
- Enabled completion of nearly all work without shutting down MBTA rail passenger service or closing I-90
- Delivered a project that revitalizes its neighborhood with improved highway, bike, pedestrian, and public transport access
For more information, contact:

Senior Principal Consultant
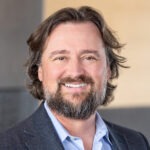
Service Leader, Geotechnical Engineering
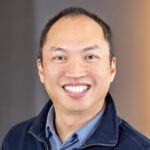
Senior Technical Expert, Geotech Engineer