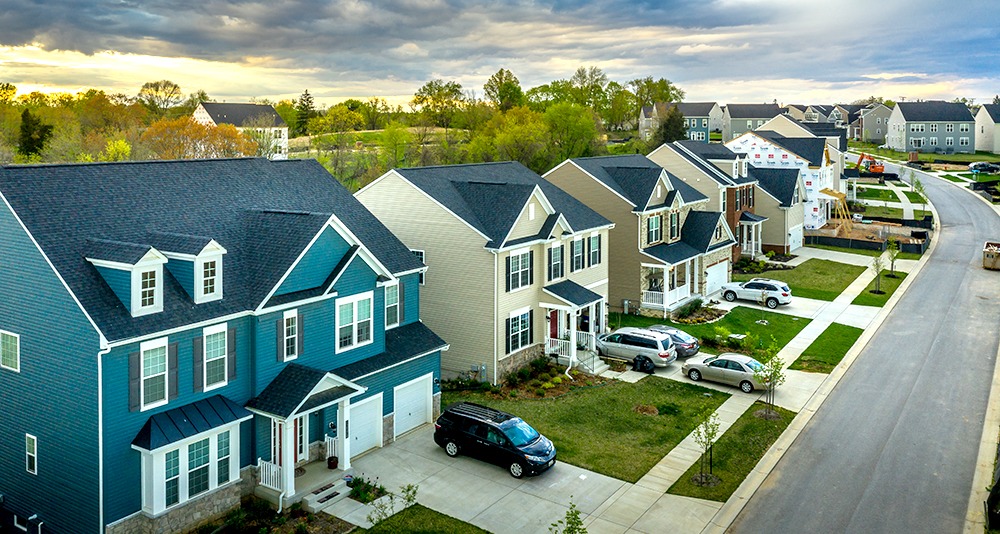
Manufacturing
We help a spray-drying company mitigate odors, preserving brand and reputation
2 years
saved client in experimenting with new equipment
$140,000
saved for client by eliminating costly equipment
Summary
- Our client had to mitigate odors coming from its facility, and turned to Haley & Aldrich to find an effective air quality solution.
- We identified the potential sources of odor and proposed solutions that would control the problem while also meeting operational and financial goals.
- We eliminated the need for costly control equipment the client was considering, saving time and money.
- We also proved that not every odor required abatement, opening the door for a renegotiation of air permits and additional operational flexibility.
- Ultimately, this work enabled the client to maintain its strong reputation in its community by thoroughly analyzing the problem and providing an effective solution.
Client challenge
Our client, a spray-drying operation, began receiving complaints from nearby residents about odors emanating from its facility. The emissions were not harmful to human health, and the facility already employed industry-standard odor abatement technology. However, the county’s health department elevated the complaints to the state environmental agency, which then required the odorous air to be mitigated. Our client knew that, given the ambiguous world of odor control, there wasn’t an obvious solution. It considered stopping the manufacture of the odor-generating products, but before taking that financial hit, the client and its attorney sought outside expertise, turning to Haley & Aldrich for our deep understanding of how community issues can damage company reputations and our commitment to finding air quality solutions aligned with our clients’ larger goals.
Our approach
Our air quality specialists needed to fix this problem, but there was no existing guidance, and state regulations only generally reference that a facility will not generate nuisance odors. We made sure to take a wide view, understanding that any solution we developed needed to meet the needs of not only our client, but also those of the community and regulators. To achieve these multiple objectives, we followed a three-stage process of identifying the potential sources of odor, evaluating the impact of these odors, and proposing odor mitigation recommendations to control the impacts while also considering the operational and financial impacts of these changes.
“There are many ways to mitigate manufacturing odors while addressing community and regulatory concerns. But stopping production or purchasing expensive technologies may hit your bottom line hard. It’s important to balance the needs of your business with those of the community and regulators so your solution doesn’t create more problems.”
Tina Berceli-Boyle, Haley & Aldrich
During the odor assessment stage, we reviewed local meteorological data and determined that the community odor complaints were directly correlated to when the manufacturer was producing specific products. We then evaluated and quantified the odor impacts through sampling and modeling. This confirmed our hypothesis developed during the odor assessment stage — that the facility was indeed the source of the odor.
With that knowledge, we could determine the best options for odor mitigation and control, which we evaluated from technical and economic perspectives. Our client ultimately settled on our proposed solution to install a thermal oxidizer, a process unit that controls air pollution, instead of continuously operating their existing control equipment for all their production lines. We recommended the elimination of existing controls and use of the thermal oxidizer only during those manufacturing processes that emitted odors — reducing costs and emissions alike. This solution met our client’s goals of keeping critical manufacturing operations running while preserving its strong brand and positive community reputation. Our team also collaborated with our client’s attorneys to successfully demonstrate to the state regulators that the solution would eliminate the nuisance odors.
Value delivered
- Provided the data the client’s attorney needed to work effectively with the state agency
- Uncovered the chemistry behind the client’s existing control equipment failure which ultimately led to the problem’s resolution
- Proved scientifically that not every odor being controlled required abatement, opening the door for a renegotiation of air permits and additional operational flexibility
- Eliminated the need for costly control equipment the client was considering that would have proven ineffective, thereby saving the client $140,000 and an estimated two years of experimentation
- Helped the client maintain its strong brand name and reputation in the community by thoroughly analyzing the problem and providing an effective solution that satisfied both the state agency and local residents
For more information, contact:
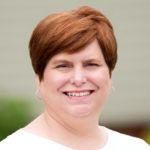
Senior Associate, Chemical Engineer
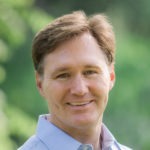
Senior Technical Expert